CNC Machining technology: application of defining characteristics of turning drilling of thin-walled workpieces
CNC machining technology: the definition characteristics of turning drilling of thin-walled workpieces Application 1, the definition of drilling
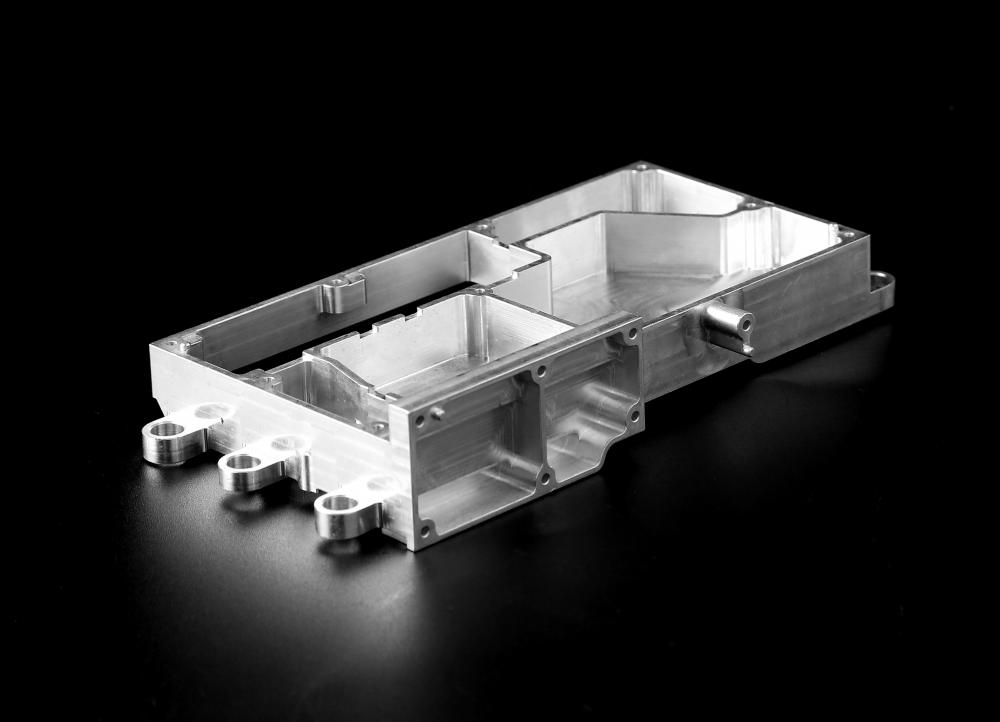
English name: drilling Definition: The drilling tool moves relative to the workpiece and makes axial feed movement, and the method of machining holes on the workpiece. Drilling is one of the most basic methods of hole processing. Drilling is often carried out on drilling and lathes, but also on boring and milling machines. Commonly used drilling machines are desktop drilling machines, vertical drilling machines and rocker drilling machines. Second, the characteristics of drilling: Compared with turning the outer circle, the working part of the drill bit is much more difficult to work on the machined surface, which causes some special problems. For example, the stiffness and strength of the drill, chip capacity and chip removal, guiding and cooling wetting and medium slip, etc., the characteristics can be summarized as follows: 1. The drill bit is easy to deflect Deflection: refers to the enlargement of the aperture, the non-round hole or the skewed axis of the hole caused by the bending of the drill bit during processing, etc., see Figure 2-6. Reason: Due to the inaccurate centering of the drill edge, the rigidity and guiding effect of the drill bit are poor, and the drill bit is easy to offset and bend when cutting. 2. Difficulty in chip removal The drilled hole has a wide chip, the size of the chip groove is limited, and when it flows out, it rubs the surface with the hole wall violently, and the hole is forced to roll into a spiral. The chip and the hole wall have greater friction, extruding, pulling and scratching the processed surface, reducing the surface quality. Even chips will be blocked in the chip groove, stuck or broken drill bits, and the tool wears quickly. In order to improve chip evacuation conditions, chip splitting grooves can be sharpened on the drill bit, and wide chips can be divided into narrow strips to facilitate chip removal. When drilling deep holes, suitable deep hole drilling should be used for processing. 3. High cutting temperature Because drilling is a semi-closed cutting, the main cutting edge near the drilling core and the cross edge have a large negative front angle, the heat generated during drilling is absorbed by the workpiece a lot, a large number of high-temperature chips can not be discharged in time, cutting fluid is difficult to inject into the cutting zone, cutting heat is not easy to dissipate. The friction between chips, tools and workpieces is high, so cutting temperatures are high, tool wear is high, and drilling usage and productivity are limited. 4. Low accuracy The drilling accuracy is low, the surface is rough, the general machining accuracy is below IT10, the surface roughness Ra value is greater than 12.5mm, and the production efficiency is also low. Therefore, drilling is mainly used for roughing or pre-machining operations. Pictured: Structural diagram of vertical drilling machine and rocker drilling machine Third, the application of drilling In single-piece and small-batch production, small holes (D<13 mm) on small and medium-sized workpieces are commonly processed by benchtop drilling machines, and larger holes (D<50 mm) are commonly processed by vertical drilling machines; The holes on large and medium-sized workpieces should be machined by rocker drilling machine, and the holes on the rotary body workpieces should be machined on lathes. In batch and mass production, in order to ensure machining accuracy, improve production efficiency and reduce processing costs, drilling dies, multi-axis drilling or combination machine tools are widely used for hole processing. Small and medium-diameter holes (D<50mm) with high precision and low roughness often require semi-finishing and finishing with expansion and reaming holes after drilling. Dongguan ganzoo Prototype Manufacturing Co., Ltd. has more than ten years of CNC machining experience, and has deep accumulation in various metal specific projects such as aluminum alloy precision parts processing, automation Equipment parts processing, etc. It is a solution provider focusing on prototypes, high-precision parts, molds, on-demand manufacturing and other one-stop services. Is an expert in Stainless Steel Tmetal Fabrication, Stainless Steel CNC Part,Medical Plastic Injection Molding If you are interested in our service or need any technical support, welcome to contact us Ms.Becky+(86)13006687216, we are happy to share our understanding of Medical Device Spare Parts with you and provide solutions for your economy Steel CNC Part service.