Hardware surface treatment is a process method that artificially forms a surface layer on the surface of the matrix material that is different from the mechanical, physical and chemical properties of the matrix. The purpose of surface treatment is to meet the corrosion resistance, wear resistance, decoration or other special functional requirements of the product. For metal castings, our more commonly used surface treatment methods are: mechanical grinding, chemical treatment, surface heat treatment, spraying surface, surface treatment is to clean, sweep, deburr, degrease, de-oxidize the surface of the workpiece, etc.
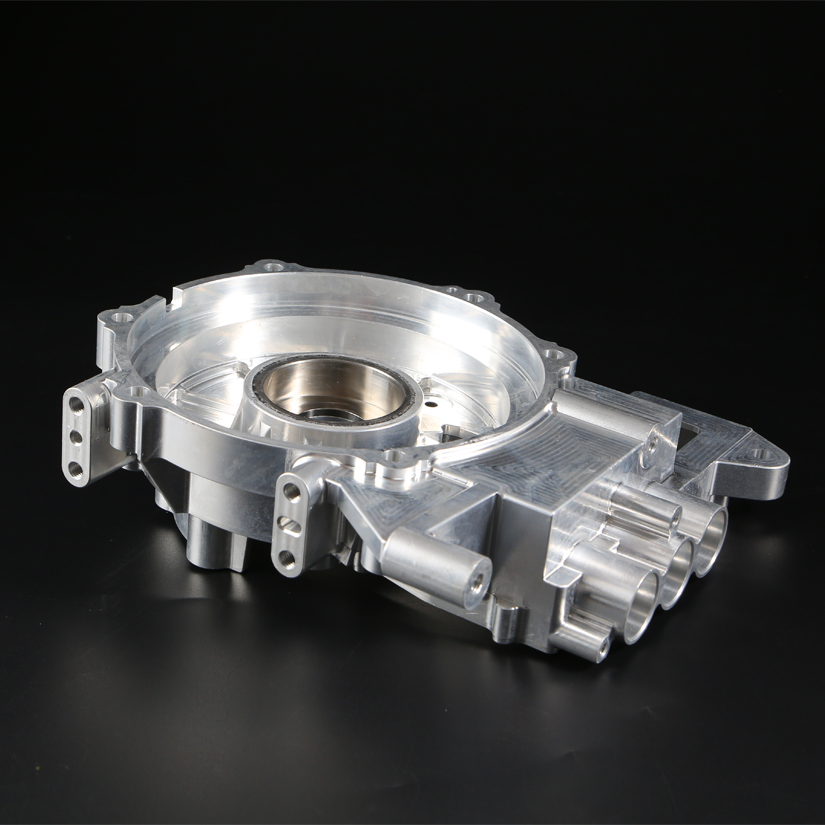
1. Manual processing Such as scrapers, wire brushes or grinding wheels. Rust and oxide scale on the surface of the workpiece can be removed by hand, but manual processing is labor-intensive, production efficiency is low, quality is poor, and cleaning is not thorough. 2. Chemical treatment Mainly the use of acid or alkaline solution and the surface of the workpiece oxide and oil chemical reaction, so that it dissolved in the acid or alkaline solution, in order to remove the surface of the workpiece rust oxide scale and oil stain, and then use nylon made of brush roller or 304# stainless steel wire (acid and alkali resistant solution made of steel wire brush roller cleaning can achieve the purpose. Chemical treatment is suitable for cleaning thin sheets. 3. Mechanical treatment It mainly includes wire brush roller polishing method, shot blasting method and shot peening method. The polishing method is that the brush roller is driven by the motor, and the brush roller rotates at high speed on the upper and lower surfaces of the strip to brush the iron oxide scale in the opposite direction to the movement of the rolled part. The brushed iron oxide scale is washed off with a closed-loop cooling water flushing system. Shot blasting cleaning is a method of using centrifugal force to accelerate the projectile and throw it to the workpiece for rust removal and cleaning. However, the shot blasting flexibility is poor, limited by the site, and there is some blindness when cleaning the workpiece, and it is easy to produce dead corners that cannot be cleaned on the inner surface of the workpiece. The equipment structure is complex, there are many wearing parts, especially blades and other parts wear quickly, maintenance hours are many, the cost is high, and the one-time investment is large. Surface treatment with shot peening, the blow force is large, and the cleaning effect is obvious. However, shot peening on the treatment of thin plate workpieces, easy to deform the workpiece, and steel shot hit the surface of the workpiece (whether shot blasting or shot peening) to deform the metal substrate, because iron oxide and iron oxide have no plasticity, peel off after crushing, and the oil film and its material together deformation, so for the workpiece with oil stain, shot blasting, shot peening can not completely remove the oil stain. Among the existing workpiece surface treatment methods, the best cleaning effect is also sandblasting. Sandblasting is suitable for cleaning with high requirements on the surface of workpieces. However, China's current general sandblasting equipment is mostly composed of reamers, scrapers, number one elevators and other primitive bulky sand conveying machinery. The user needs to build a deep pit and make a waterproof layer to install machinery, the construction cost is high, the maintenance workload and maintenance cost are very large, and a large amount of silica dust is generated during the sandblasting process that cannot be removed, which seriously affects the health of operators and pollutes the environment. Foreign sand suction machine as a machine to transport sand volume, sand suction machine is actually a super large vacuum cleaner, with a thicker conveying pipe to connect the hopper with the sand suction machine, the sand sucked into the storage tank, sand suction machine is characterized by construction difficulty and process than the bucket elevator is simple, and convenient and easy to control, less maintenance, but large power consumption, sand suction machine at present there are several manufacturers specializing in making sand suction machine in China, but the technology is relatively not mature enough, so the vast majority of surface treatment enterprises mainly use bucket elevators. Need to do the spraying process of the factory in the selection of sand conveying equipment and dust removal equipment must fully consider the actual situation of production, try to choose power relative to the production of larger equipment, because the equipment of shot blasting industry is generally lost faster, long-term use after this or that problem will affect production a lot, the selection of equipment with larger power will greatly reduce the time and cost wasted in future maintenance. The insufficient power of the dust removal equipment not only damages the health of workers, but also seriously affects the visibility of the sandblasting room, and the dust cannot be discharged out, which also affects the quality of the sand itself and affects the surface roughness of the workpiece. The manual sandblasting room should be designed according to the actual situation relative to the space that accommodates the workpiece, not too restrained, otherwise it will affect the manual operation of workers, and the lighting conditions must be good, and the sand throwing can be placed outdoors for drier areas. 4. Plasma treatment Plasma, also known as plasma, is a collection of positively charged positive particles and negative particles (including positive ions, negative ions, electrons, free radicals and various active groups, etc.), of which positive and negative charges are equal so it is called plasma, which is the fourth state of matter in addition to solid, liquid and gaseous states - plasma state. The plasma surface processor is composed of plasma generator, gas delivery pipeline and plasma nozzle, plasma generator generates high-pressure high-frequency energy in the nozzle steel tube is activated and controlled glow discharge to produce low-temperature plasma, with the help of compressed air to spray plasma to the surface of the workpiece, when the plasma and the surface of the treated object meet, object changes and chemical reactions are produced. Dongguan ganzoo Prototype Manufacturing Co., Ltd. has more than ten years of CNC Machining experience, and has deep accumulation in various metal specific projects such as aluminum alloy precision parts processing, automation Equipment parts processing, etc. It is a solution provider focusing on prototypes, high-precision parts, molds, on-demand manufacturing and other one-stop services. Is an expert in Stainless Steel Tmetal Fabrication, Stainless Steel CNC Part,Medical Plastic Injection Molding If you are interested in our service or need any technical support, welcome to contact us Ms.Becky+(86)13006687216, we are happy to share our understanding of Medical Device Spare Parts with you and provide solutions for your economy Steel CNC Part service.